In modern carpentry and furniture manufacturing companies, an increasing share of machining is performed using computer-controlled CNC machining centers. This is mainly due to the situation on the labor market, but also to the customer’s pressure for higher quality products. CNC technology, together with appropriately selected software, significantly simplifies a number of tasks and opens up new possibilities and procedures in production, all while saving time and maximum accuracy of machining. Shank tools of various constructions and shapes are mainly used for these machines. The basic characteristic of each tool is the geometry of the cutting edges adapted for machining a specific type of material. It is also very important to know the correct setting of cutting conditions, ie chip thickness, cutting speed, feed speed, depth of cut, and especially their current combination depending on the material being machined. With a growing emphasis on performance, the issue of high-speed machining is very current, where the cutting speed reaches up to 100 m/s, which places even higher demands on the tools used. For their reliable work and quality machining of parts, it is necessary to know the cutting forces acting on the workpiece and the tool in the individual planes depending on the fiber cutting angle, which changes in the case of rotary machining. Within the ROTCUT project, rotary cutting will be experimentally investigated from different points of view. The most important conclusions will be drawn from the images taken by high-speed cameras, where it will be possible to monitor the chip separation itself, and using a dynamometer that can accurately record the forces in the individual axes. The measurement of cutting forces takes place in three mutually perpendicular directions: parallel to the cutting speed vector, perpendicular to the cutting speed vector in the horizontal direction and perpendicular to the cutting speed vector in the vertical direction. The data obtained from the hardwood machining tests performed on a CNC machine will then be analyzed and compared with conventional methods of calculation and the finite element method. The goal of the experiments is to calibrate a model that is capable of predicting cutting force and chip formation.
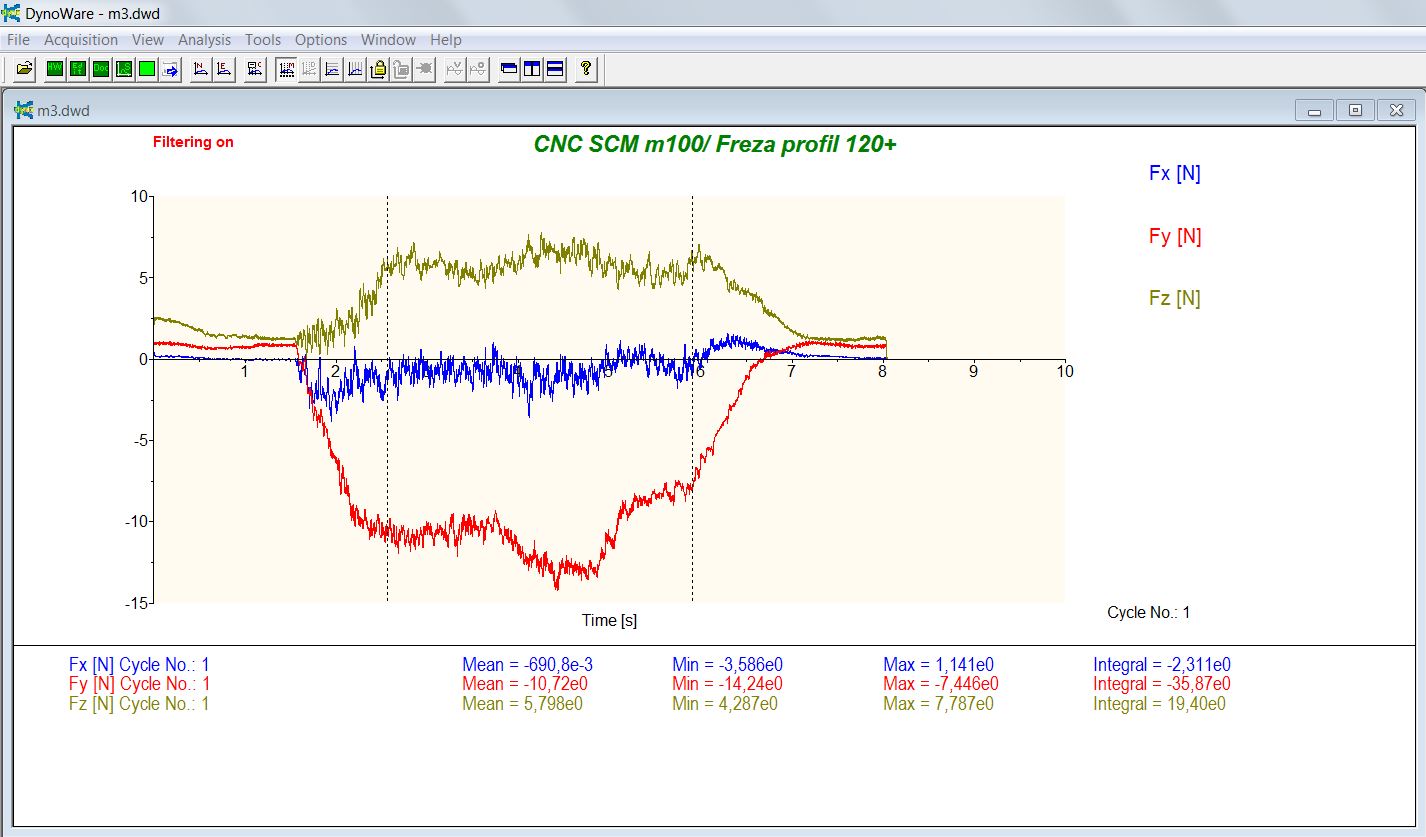
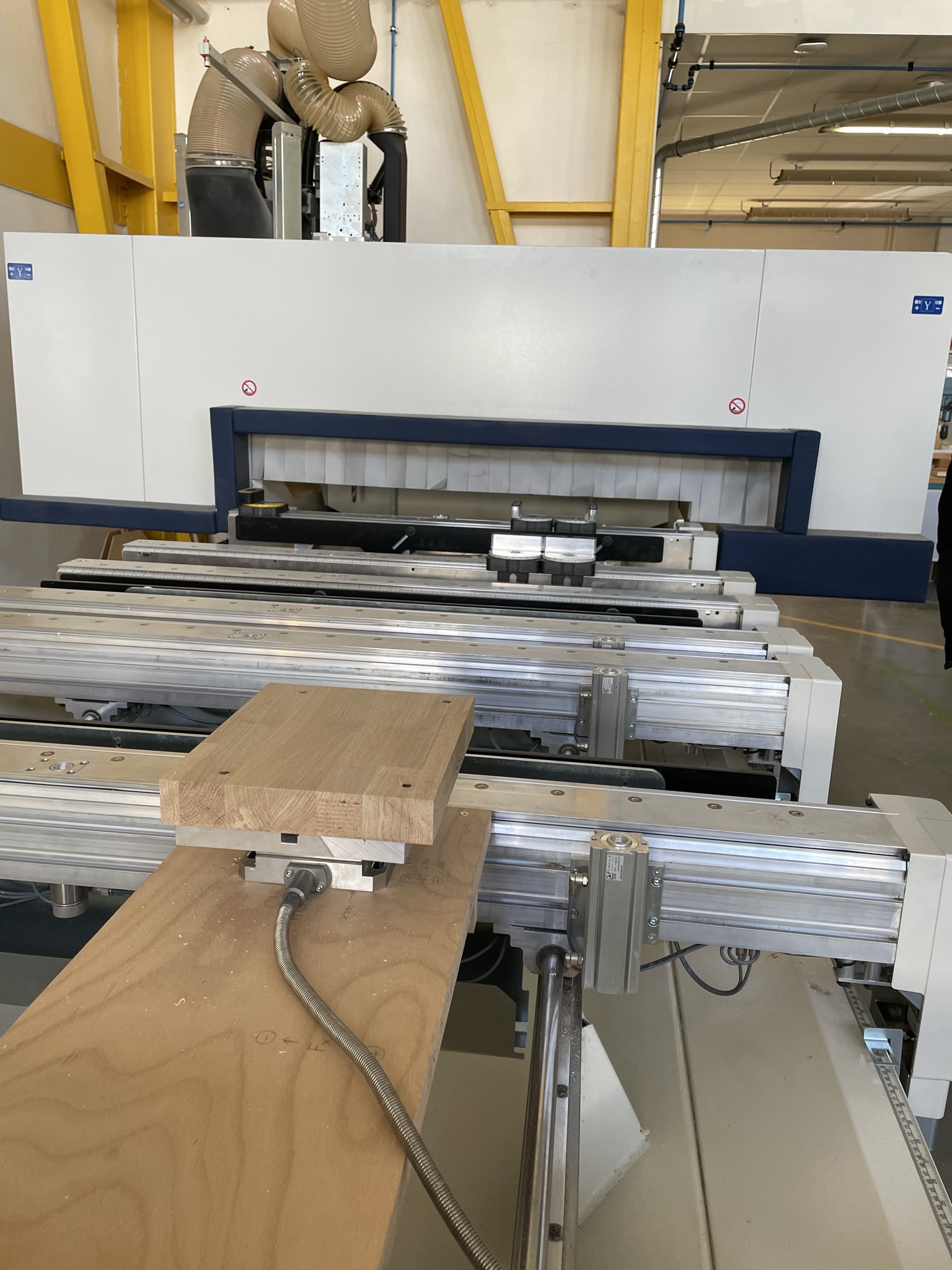
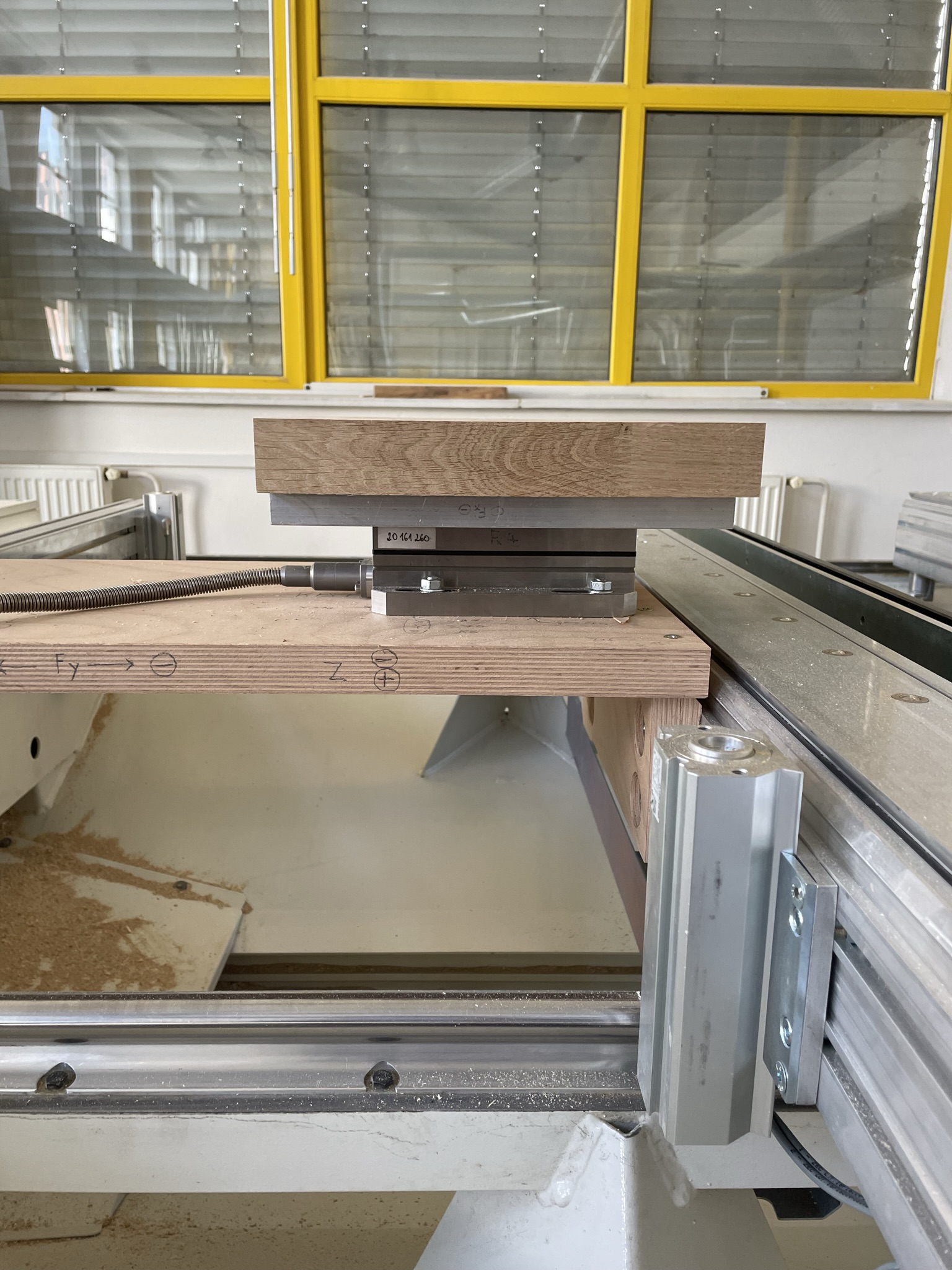
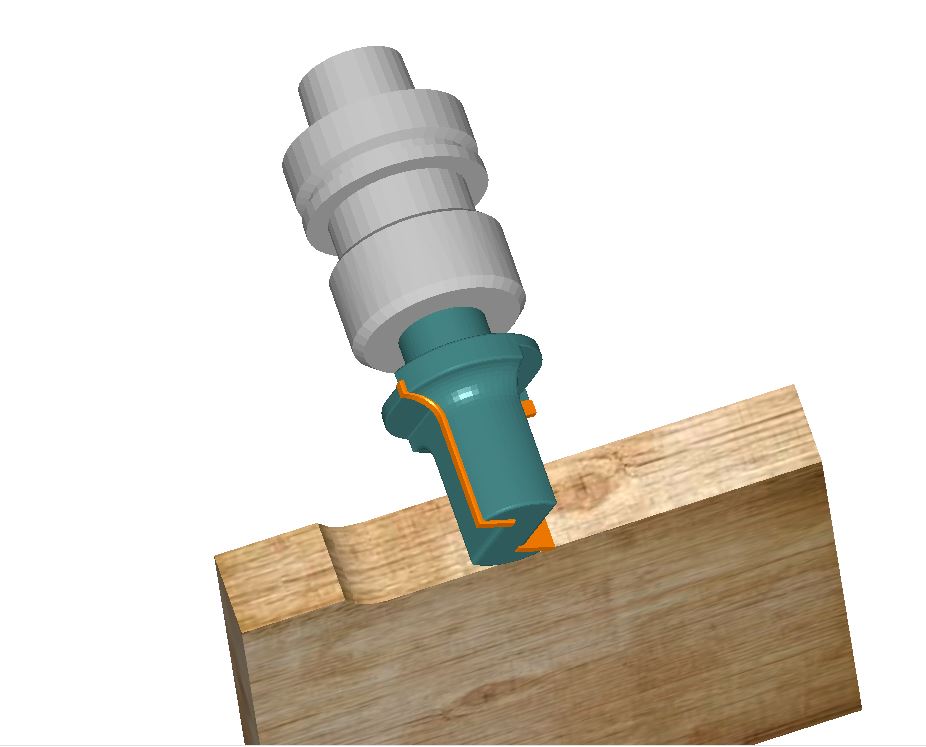