When optimizing the high-speed machining of hardwoods by using of rotary cutting tool is helpful to analyse, beside the force response of machined specimens, also the deformation field near the cutting edge. Such analysis we perform as a non-contact one by using of digital images and slow motions of specimens acquired by high-speed cameras during the machining. The cutting of chips is slowed down to 5000 times. The image data are processed by digital image processing technique that allows tracking of any point (pixel) movement on digital images acquired in time sequence. Additionally to the deformation field, the approximate dimensions and shape of cut chips can be determined. Both deformation field characterizing and chip dimensions and their shape are prerequisites for experimental verification of numerical model and its calibration.
We apply the approach starting from (1) approximation of rotary machining by means of linear machining with various wooden fibres orientation to specimen’s movement direction (cutting tool is static), to (2) analysis of machining with rotary movement of cutting tool (specimen is static). The pilot experiments approximating the rotary cutting are already done. The example of outputs is displayed on the Figure 1.
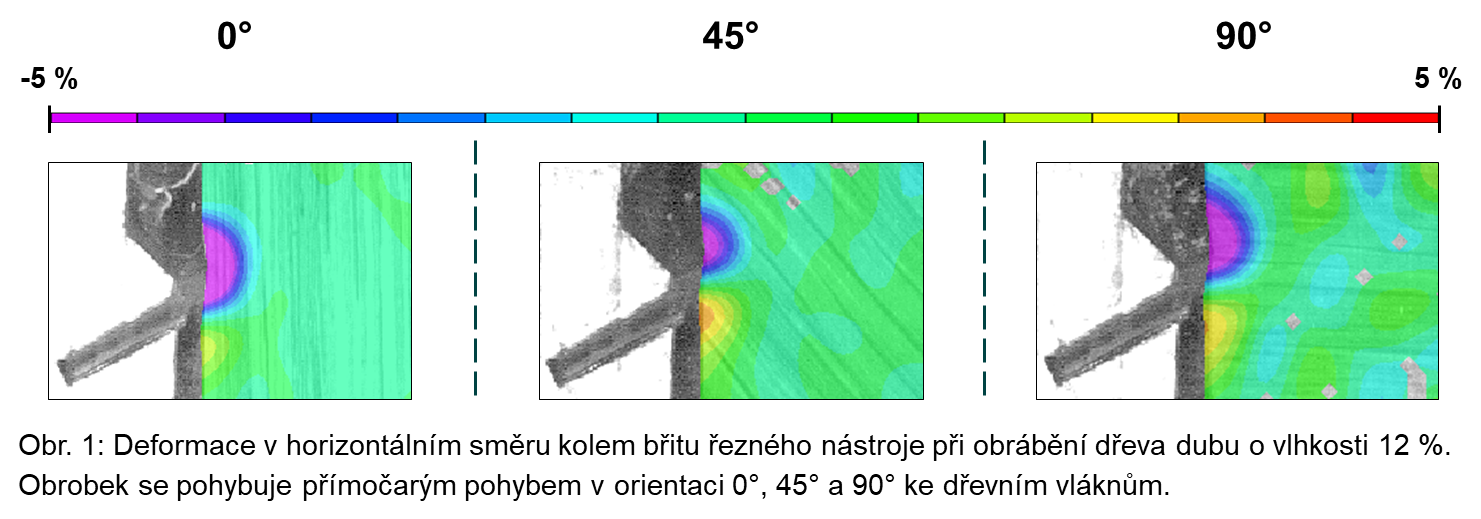
The deformation field was calculated for captured time moments and visualized as coloured contour maps where the individual colours represent the level of deformation magnitude. These contour maps revealed that orientation of wooden fibres direction to cutting velocity vector affected the ratio of tensile deformation in front of cutting tool (i.e. level of pulling out of fibres in front of cutting edge) and compressive deformation behind the cutting tool (i.e. level of specimen surface compression behind the cutting edge). Thus, the deformation near the cutting edge during the passing through the cut material will be variable; however, the absolute magnitude of this tensile and compressive deformation is approximately constant. The slow motions below the Figure 1 show the different shape of cut chips for various wooden fibres orientation to specimen’s movement direction. It is apparent that with increasing angle between the wooden fibres direction and specimen’s movement direction (from parallel to perpendicular orientation) the cut chips’ dimensions decrease.
We have also the pilot slow motions of machining with rotary movement of cutting tool acquired by high-speed camera (Slow motion 1). The machining of dry spruce wood by the double knife milling tool was captured.